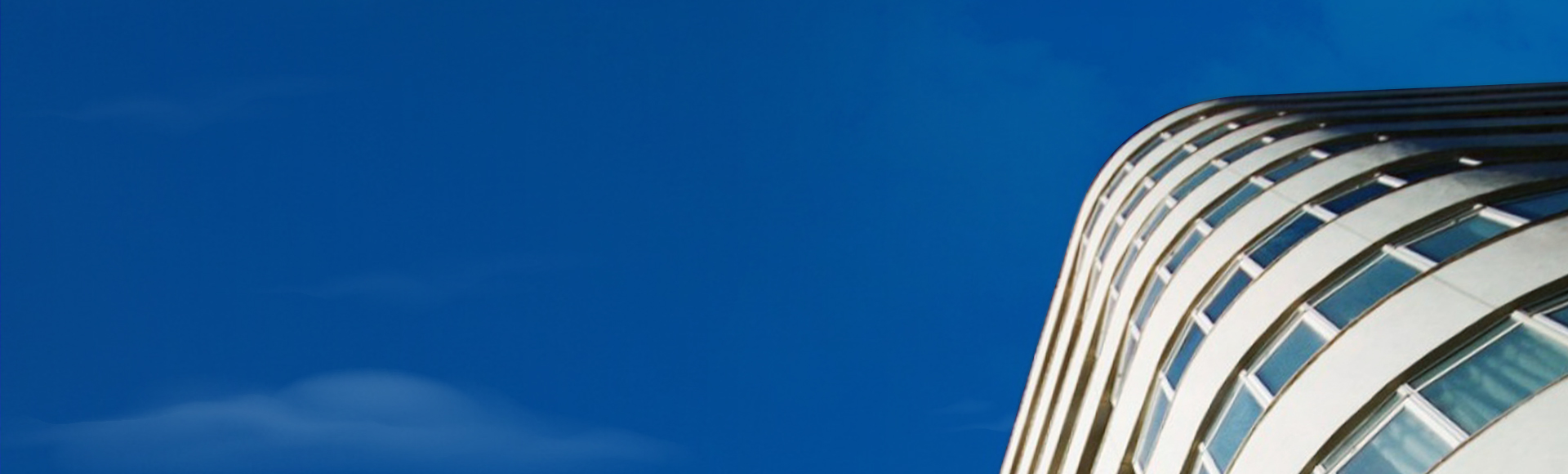
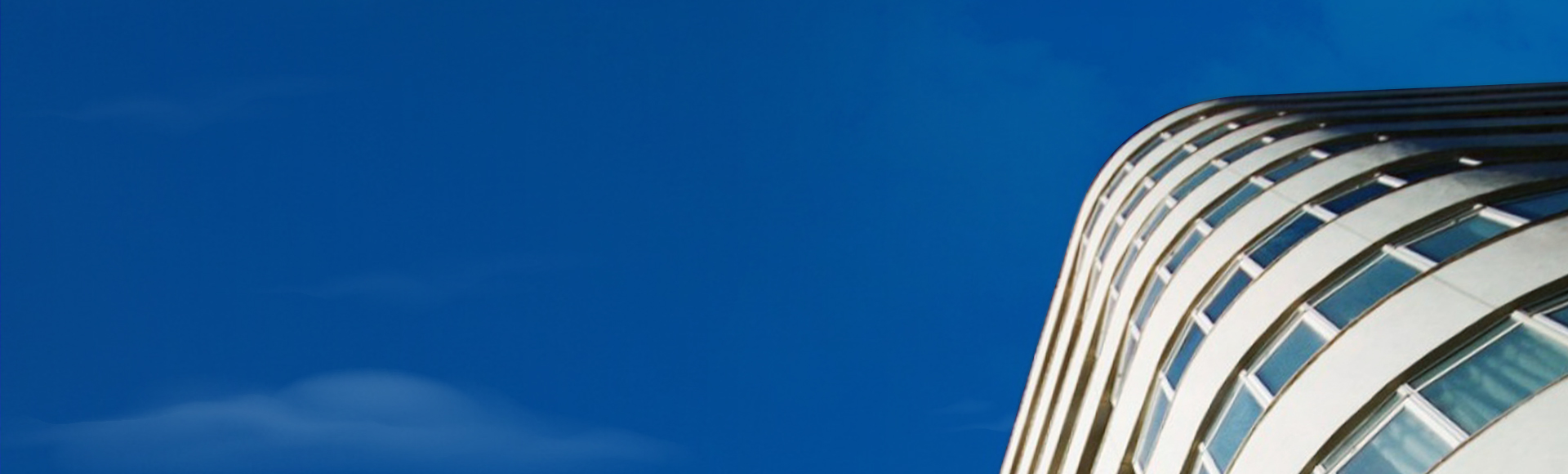
【氧化铝纤维厂家】自动化、数字化时代下,我国航空复材产业链如何实现国产化?
复合材料广泛应用于飞机工业,使工程师克服了单独使用材料时遇到的障碍。组成材料在复合材料中保持其特性,不溶解或以其他方式完全融合在一起。这些材料一起创造了一种改善结构性能的“混合”材料。
轻质、耐高温复合材料的开发将使下一代高性能、经济的飞机设计成为现实。使用这种材料将减少燃料消耗,提高效率,降低飞机的直接运营成本。
复合材料可以形成各种形状,如果需要,纤维可以紧紧缠绕以增加强度。复合材料的一个有用的特性是它们可以分层,每层中的纤维都朝着不同的方向运动。这使得工程师可以设计具有独特性能的结构。例如,一个结构可以被设计成在一个方向弯曲,而不是在另一个方向弯曲。
航空复合材料的发展阶段
1970年,复合材料首次应用至航空航天行业中,其应用范围从最开始的舱门、口盖、整流罩等发展到目前已经应用于机翼、机身等主要承力结构;同时,随着伴随碳纤维等复合材料技术工艺不断提升,高性能复合材料的使用和替代范围进一步扩大,部分飞机复合材料比重已达到50%以上。
1、民用领域
复合材料在飞机上的应用经历了前缘-口盖-整流罩-扰流板-升降舵-方向舵-襟副翼-垂尾-平尾-机身和机翼等主承力结构应用的过程。复合材料应用部位已由飞机的非承力部件及次承力部件发展到主承力部件,并向大型化、整体化趋势发展。
我国民用航空器中复合材料占比不断增加,从最开始的波音757/767复合材料占比4%到波音787/空客A350的复合材料占比50%以上,复合材料在航空器制造中的应用不断增加。
2、军用领域
复合材料在改善飞机机体结构,降低结构重量,提高隐身能力等多个方面有着自己特有的贡献因此广泛应用于战斗机中。发达国家较早就将复合材料应用于战斗机制造中,美国F-22实际使用碳纤维比例高达20%,F-35中复合材料的使用比例达到了35%,具体在蒙皮和机翼结构和机体结构部件上,大量的使用了碳纤维复合材料。目前,中国的战斗机用复合材料的应用还有待提高,歼-11B用复合材料占比约为12%,距离发达国家还有一定的距离。
我国民用、军用飞机数量呈不断上升趋势,根据交通运输部的统计数据,截至2021年,民用飞机数量为4054架;根据《worldairforces2022》统计,截至2021年,我国军用飞机数量共有3285架,较2020年增加25架。在此趋势下,我国航天用复合材料使用量将不断增加。
随着我国航空器产品的不断升级,对于航空器用复合材料也提出了轻质、耐磨损、耐腐蚀、耐低温、耐高温、抗氧化等要求。未来,我国航天用复合材料将会朝着高性能化、低成本化、多功能化发展。
“自动化”进程正在加速
随着复合材料、增材制造在国产民机上的应用比例越来越高,在“生产端”的体现便是引入更多自动化设备。以复材的批量生产为例,随着碳纤维复合材料零部件的尺寸、厚度不断增加,工艺上对铺贴的精度要求越来越高,而且还是不同的方向铺贴。为了确保质量、减少人为因素,从手动铺带到自动铺带/铺丝就成了行业的必然趋势。
以此为起点,后续如复材零部件的转运、加工、检测等工序也在向着自动化迈进。
“数字化”是行业趋势
近日,在第八届航空材料与制造工艺国际论坛(下文简称航材论坛)上,来自波音、西门子等企业的专家重点关注了生产制造环节的自动化、数字化。
比如增强现实AR技术在装配上的应用,利用人工外骨骼等设备来助力人工作业、降低作业强度,通过人机交互技术来充分发挥人工和机器人/自动化设备的各自优势,通过自动化系统的仿真来提高生产效率、降低系统的故障率,通过数字化工具搭建生产标准流程,对流程仿真、模拟、验证进行量化分析并得出优化建议等。
数字化在航空材料领域的应用,不单单是这些制造阶段,上溯到前设计阶段也是离不开“数字化”的助力与赋能。
设计人员可通过数字化工具(比如有限元分析软件、辅助设计软件、工业软件等)来加强对新材料、新工艺的了解,将其优势与缺陷全方位地展现出来,进而提高开发速度、缩短开发周期、降低开发成本,助力工程师更高效地找到结构设计与材料性能上的最优解。
向着“数字化”的迈进,还包括与大数据、AI人工智能、机器学习等近年新兴数字技术相结合。比如面对模拟仿真工作、试验过程中产生的海量数据,通过数字技术来帮助技术人员更高效地完成对数据的整理、分析等工作。
不仅如此,这场席卷航空制造业的“数字化”正从设计、制造等阶段,不断外延拓展。比如在关乎一型航空产品成败的适航审定阶段,目前国外在适航审定思路上就正从传统的“一构型一检”向着数字化工具之下的模拟和分析方法转变。而随着这条“数字化”必由之路的不断延伸,它正在将设计、制造、装配、测试、适航认证、维护、改型升级等全链路环节逐步打通、融合,形成“一体化”。
国产航空复材的“工业化时代”
通过论坛上专家的报告发言,我们已经了解到国产民机在复材、增材制造上的应用迈出了第一步,比如C919上复材应用比例达到了12%。但数字背后的另一个事实是这些复材的原材料都还是来自国外。所以,在未来的CR929上,中国商飞表示在使用进口原材料的同时也将使用国产材料,“将国产材料纳入到了整个研制过程中”。
不过,相较于国外航空复材上万吨的年产量,我国航空复材产量规模偏小,尚未进入大批量的工业化生产阶段。对此,与会相关专家都在强调,工艺性能、PCD文件(“材料生产过程控制文件”)是国产航空复材能否迈过工业化批产这一关的关键所在。否则会导致质量稳定性不佳(表现为不同批次材料成分或性能波动较大、报废率高、生产效率不高、加工成本上涨乃至是无法装机应用等)。有专家指出“一些国产航空材料获得了批准,但PCD准备上不够或是推广的不好,产品的稳定性较差”。
可见,一款航空复材的成功,不单单是在实验室阶段有着出色的性能参数和获得认证批复,还要看当它的“工艺性能”,在进入到批量工业化生产阶段后能否有着各批次的质量稳定,同时还兼顾了生产效率、生产成本等。
“打造复合材料产业链”
对于我国航空制造业来说,在航材领域的目标不单单是国产航空复材的大批量工业化生产,还在于“打造复合材料产业链”,培育形成全产业链上下游的核心供应商,包含材料的供应商、原材料的供应商和工艺材料的供应商等,它们的材料要覆盖主要材料规格,质量持续达标稳定、严格遵循认证标准、具备国际竞争力。
这些材料既包括复材核心的T300级的碳纤维、T800级碳纤维、玻璃纤维等,也包括复材制造过程中所需的工艺材料、辅助材料等。
此外,还有这条产业链中尤为重要的一环——设备供应商,包括生产设备、铺贴设备、成型设备、加工设备、检测设备等。目前相关的关键性国产设备正经历从“解决有无”到“好用与否”的蜕变,而这也是制造商与国产设备供应商间的紧密协同、“双向奔赴”、不断迭代的过程。
展望未来,随着国产设备的“蜕变”日臻完善,国产航空复材的产量不断提升并更大范围地使用,将给国产军民机带来性能与经济性上的优势。
如何实现“国产化”?
但这样的“国产化”之路绝非坦途,要直面前方坎坷,冲破技术迷雾,不断攻克一个个难题和挑战,不断向前不断取得新的突破。
这其中既包括我国民机在复材、增材制造上的应用相较于波音、空客还有不小差距,也包括技术领域与一流之间对标时,在基础理论、关键工艺技术、高端装备、核心元器件、商用软件和产业应用等多方面存在的差距与短板。
而这样的前路,又将是不断超越自我的求索之路,不断向前、不断拓展边界。需要我们不断增强对材料的认识、认识它的特性与缺憾,不断挖掘性能潜力,并梳理创立与之配套的一系列规范、准则、要求、标准和体系等。
特别是相比于业界对铝、钛等传统航空材料特性、工艺、缺陷等方面的相对全面了解,不论中外对复合材料、增材制造都还有着太多未知和迷雾,都需要大量的基础研究、更进一步的科研来“掌握它的缺陷”。由此才能最大限度地释放出新一代航空材料、制造工艺对航空技术的强大推动力。
放眼我国航空材料、航空制造技术的前路,是追赶、是超越、是求索、是创新,这是我国航空制造业转型升级的必由之路。前路虽“道阻且长”,但“道阻且长,行则将至;行而不辍,未来可期。”
来源:贤集网
关键词:#氧化铝纤维 #东珩国纤 #氧化铝连续纤维 #氧化铝纤维毡 #氧化铝纤维毯 #氧化铝纤维纸 #耐火材料 #隔热材料